In the modern packaging industry, box corner labeling machines have become essential for improving production efficiency and ensuring product quality. With the wide variety of options available in the market, choosing the right labeling machine to meet your specific needs is a crucial decision for factory owners and procurement managers. This article will guide you through the process of selecting the most suitable box corner labeling machine to help you make an informed decision.
1. Identify Your Production Needs
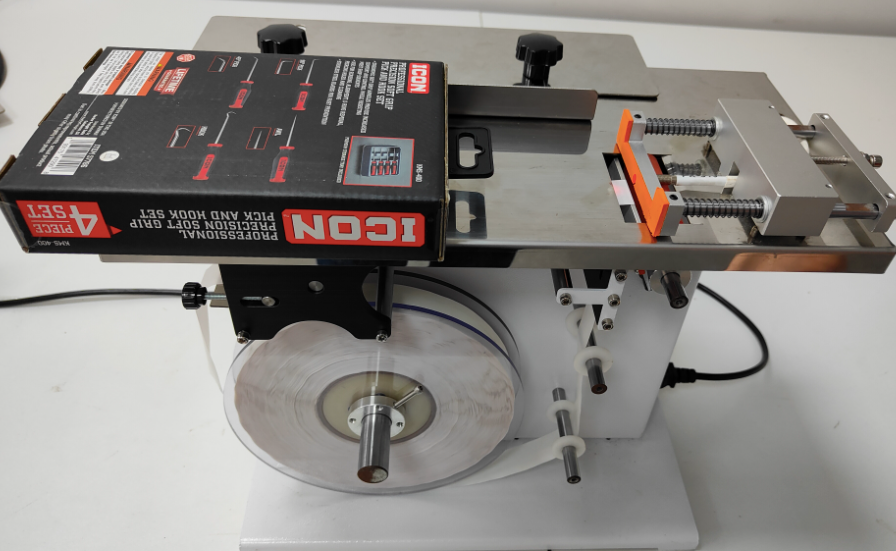
Before choosing a labeling machine, it is important to clearly define your production requirements:
- Production Scale: How many boxes need to be labeled per day or per hour?
- Box Specifications: Are your packaging box sizes varied? Selecting a machine that can handle different box sizes will provide more flexibility.
- Labeling Type: Do you need single-side labeling or multi-side labeling?
By clarifying these needs, you can narrow down the options to models that meet your capacity requirements.
2. Focus on Labeling Accuracy and Speed
Labeling accuracy and speed are key factors that determine production efficiency and product quality. High-accuracy labeling machines ensure that each label is precisely applied in the correct position, reducing misalignment and bubbles.
- Labeling Speed: Different models process a varying number of boxes per hour. Choosing a machine with a speed that matches your production line is essential. For example, a machine that labels up to 3,000 boxes per hour can meet the needs of most small to medium-sized factories.
- Labeling Accuracy: It is recommended to choose a machine with an adjustable positioning platform to ensure consistent label placement and uniform product appearance.
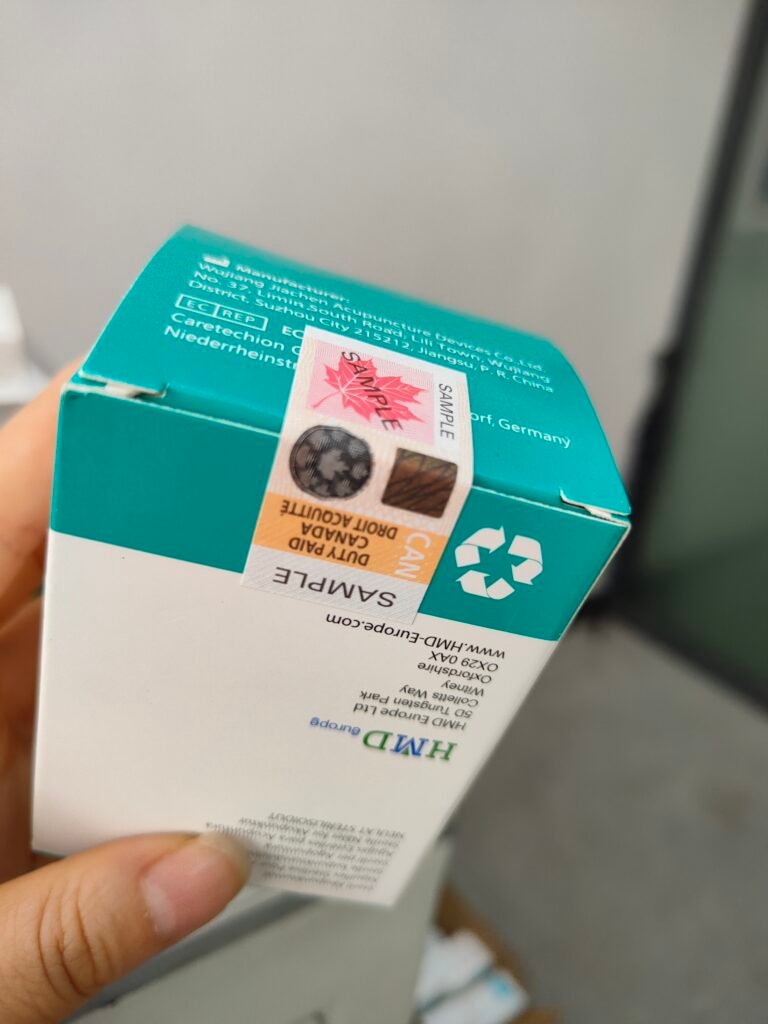
3. Ease of Operation
Workers on the production line need to operate the labeling machine frequently, so ease of use directly impacts production efficiency and employee experience. A high-quality labeling machine should have the following features:
- User-Friendly Operation: A clear and straightforward interface that workers can easily learn and use.
- Simple Maintenance: A machine with a simple design and low failure rate can reduce downtime and maintenance costs.
4. Machine Stability and Durability
Choosing a stable and durable labeling machine can provide long-term support for your production line. A high-quality labeling machine should have the following:
- Sturdy Structure: Ensures the machine remains stable during long periods of high-load operation.
- High-Quality Materials: Made with durable materials to minimize part wear and replacement frequency.
5. After-Sales Service and Warranty
Regardless of the machine’s quality, reliable after-sales service is essential for worry-free production. Choose a supplier that offers a long-term warranty and professional after-sales support to ensure any issues can be quickly resolved, preventing production delays due to downtime.
6. Consider Cost-Effectiveness
Finally, when selecting a labeling machine, it is important to balance cost and performance. A machine with a low price but insufficient performance may result in hidden costs over time, while a machine with high performance but an excessive price can strain your budget. Therefore, choosing a labeling machine with a balance of performance and cost is crucial.
Conclusion
Choosing the right box corner labeling machine can not only improve production efficiency but also help factories reduce labor costs and optimize production processes. Defining your production needs, focusing on labeling accuracy and speed, ensuring ease of operation, machine stability and durability, and reliable after-sales service are all key factors to consider when making your purchase. We hope this guide helps you make the best choice and drives your production line toward greater efficiency and stability.